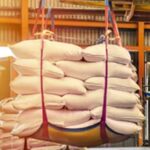
Imagine 100% productivity of your rice mill machine
December 2, 2024Basics of a Rice Mill Machine Process Flow
Rice is one of the most important crops as it is a staple food across the world. Rice mill machine facilitates production of edible polished, milled, or white rice by removing the bran and husk from harvested rice. This blog is relevant for all those interested in setting up a rice mill for the first time and for the ones who want to expand their existing milling machine setup for forward integration or backward integration.
About Rice Milling
When is it done?
The rice milling process is the last and most critical stage in producing high-quality milled rice. It plays a key role in determining both the quantity and quality of the final product. That’s why choosing the right rice milling machines is essential for success.
What is the process?
In the earlier days, rice was milled through the process of friction and then ground between two stones, called “stone milling”. It is a traditional practice which is time consuming and gives a relatively lower and coarse output. The industry today has moved on to “Roller Milling” which uses a set of mechanical, semi-automatic and automatic machines to produce high quality produce with lesser wastage.
The by-products of rice milling process are rice husk, rice germ and bran layers, and fine brokens. In today’s automated milling process the ideal composition of outputs achieved are: 20% husk, 8−12% bran depending on the milling degree and 68−72% milled rice or white rice depending on the variety. Total milled rice contains whole grains or head rice, and brokens.
Understanding the size of a Mill
The size of a rice mill is estimated by the paddy input capacity.
Small Rice Mill or as the industry terms it “mini rice mills” are mills with an input capacity of 1-5 tonnes per hour.
A medium sized rice mill will have a paddy input capacity of around 5-8 tonnes per hour.
A large sized or full size mill is one with an input capacity of over 10 tonnes per hour.
Process of Milling
1. Paddy Cleaner
This is a pre-cleaning stage, where the paddy (just entering the mill) is separated from foreign materials such as straw, weed seeds, and soil. The capacity of the paddy pre-cleaner milling machine is normally 1.5 times the milling capacity.
2. Destoner
A destoner machine uses gravity, density difference, and airflow to separate materials based on their weight. It cleans the Paddy from heavy particles like stones.
If the paddy is not thoroughly cleaned before hulling, the efficiency of the huller will be reduced.
3. Dehusking or Husk Seperator
Brown rice is produced by removing the husk from rough paddy rice. This rice mill machine removes the husk by friction as the paddy pass between two abrasive surfaces that move at different speeds. Husk accounts for 20% of the paddy weight and an efficient husker should remove 90% of the husk in a single pass.
4. Paddy Seperator
The amount of paddy should not be more than 10%. Paddy separators work by making use of the differences in specific gravity, buoyancy, and size between paddy and brown rice.
5. Whitening
The Rice Whitener removes the bran layer and the germ from the paddy to produce white rice. The bran layer is removed from the kernel through either abrasive or friction polishers. To reduce the number of broken grains during the whitening process, rice is normally passed through two to four whitening machines connected in series.
6. Silky Polishing
To enhance the luster of rice, a fine mist of water is added during the final polishing stage. A friction-type whitening machine delivers this mist, improving the rice's shine by removing dust. This final polish ensures the rice is pristine and ready for sale.
7. Grading White Rice
The next in the rice mill machine sequence is a sortex or a color sorter. Here, the output is graded on the basis of length, thickness, brightness. We separate the Head rice kernels (75-80% of the whole rice grain) from the broken heads.
8. Bagging of Rice
Packaging systems are available to cater as per need basis-- for direct end consumer, which could be in 500g, 1 kg, 5 kgs or 10 kgs to packaging for wholesale or bulk- which is in sacks of 20 kgs or 50 kgs (as per requirement). Silos are also used for storage. While most rice mills use a manual mechanical weighing system, automated systems are also available.
Click here to see the Basic Process Flow at a Rice Mill!
Please note all milling machines come in mechanical, semi-automatic and automatic variants. Depending on the rice mill machine price the customer has allotted.