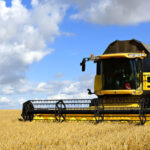
Combine Harvester: Unlocking Efficiency in Rice Harvesting
January 15, 2025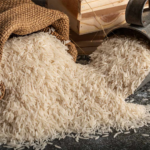
Understanding Rice Breakage: Causes and Solutions
February 17, 2025PROACTIVE MAINTAINENCE OF YOUR RICE MILL MACHINE
Maintaining the efficiency and longevity of your rice mill machines is crucial for the success of any rice milling business. Proper upkeep ensures that these machines operate at peak performance, minimize downtime, and maintain product quality. This is especially critical for us, where the demand for high-quality output and consistent operation is non-negotiable.
Why is Maintenance of Rice Mill Machines Important?
-
Enhanced Efficiency and Productivity
Regular maintenance prevents breakdowns and ensures that machines run smoothly, thereby increasing operational efficiency. Efficient machinery leads to higher productivity, which is essential in meeting the growing demand for rice in African markets.
-
Prolonged Equipment Lifespan
Routine checks and timely repairs reduce wear and tear, extending the lifespan of expensive rice milling equipment. This saves costs in the long run and ensures a better return on investment.
-
Improved Product Quality
Rice mill machines must perform precise operations such as cleaning, husking, and polishing. Well-maintained machines produce rice of consistent quality, meeting the high standards required in international markets.
-
Minimized Downtime
Breakdowns can disrupt production schedules, leading to delays and financial losses. Preventive maintenance reduces the likelihood of sudden malfunctions, keeping operations running smoothly.
Key Components Requiring Regular Maintenance in Rice Mill Machines
Below is a detailed look at the key components of rice mill machines that require regular maintenance.
1. Pre-Cleaning Equipment
Pre-cleaning equipment plays a vital role in removing impurities such as stones, dust, and husks from raw paddy before processing. This initial step ensures better machine efficiency and product quality.
Maintenance Tips
- Inspect Screens and Brushes Regularly: Check for any damage or clogging in the screens and brushes. Replace worn-out parts promptly to maintain efficiency.
- Clean Thoroughly: Ensure the equipment is cleaned after each use to prevent clogging and contamination, which can compromise rice quality.
- Tighten Loose Components: Periodically check and secure any loose nuts, bolts, or other fittings to avoid operational issues.
2. Dehusking Machines
Dehusking machines separate the husk from the paddy, preparing it for further processing. This step is
critical for achieving efficient husk removal without damaging the rice grains.
Maintenance Tips
- Check Rubber Rolls: Inspect the rubber rolls for signs of wear or damage. Replace them as needed to ensure optimal performance.
- Align Rollers Properly: Misaligned rollers can reduce dehusking efficiency and increase grain breakage. Regular alignment checks are essential.
- Lubricate Bearings: Apply appropriate lubrication to reduce friction and prevent wear on moving parts.
3. Paddy Separators
Paddy separators distinguish between unhusked paddy and brown rice, ensuring only properly dehusked grains proceed to the next stage.
Maintenance Tips
- Calibrate for Optimal Separation: Periodically calibrate the machine to maintain accuracy in separation, especially when processing different rice varieties.
- Inspect for Wear and Tear: Check for damaged or worn-out parts that may hinder functionality and replace them promptly.
- Clean Moving Parts: Prevent residue build-up by cleaning regularly to maintain smooth operations.
4. Polishing Machines
Polishing machines enhance the appearance of rice grains, giving them a shiny, polished finish that appeals to consumers.
Maintenance Tips
- Monitor for Residue Build-Up: Residue inside the polishing chamber can affect grain quality and machine efficiency. Clean the chamber regularly.
- Replace Abrasive Parts: Worn-out abrasive components can reduce the polishing
quality. Replace these parts as necessary. - Inspect Motor and Bearings: Ensure the motor and bearings are functioning smoothly and lubricate them to avoid overheating or breakdowns.
5. Conveyor Systems
Conveyor systems are essential for transporting rice and by-products between different processing units efficiently.
Maintenance Tips
- Check Belts for Fraying: Inspect conveyor belts for signs of fraying, tearing, or misalignment. Replace damaged belts immediately.
- Lubricate Moving Parts: Proper lubrication prevents friction and wear in pulleys, rollers, and bearings.
- Tighten Components: Secure any loose bolts or fasteners to prevent disruptions during operation.
- Inspect for Blockages: Remove any obstructions to ensure a smooth flow of materials across the conveyor.
Scheduled Tasks for rice mill machine maintenance
- Implement a Maintenance Schedule
Create a detailed plan for routine inspections and servicing of
machinery. Assign qualified technicians to execute the schedule efficiently.
- Train Personnel
Ensure that machine operators are trained to handle equipment properly and identify potential issues. This reduces the likelihood of operator-induced damage.
- Use Genuine Spare Parts
Always replace damaged components with genuine parts from trusted suppliers. Counterfeit parts may compromise the machine’s performance and safety. Here is where Indian companies can be a game changer for African market.
- Monitor Performance Metrics
Track metrics such as throughput rate, energy consumption, and output quality to identify irregularities early.
- Maintain Clean Working Conditions
A clean and organized workspace minimizes contamination risks and enhances operational safety.
Benefits of Proactive Maintenance
-
Economic Growth
Efficient rice mills contribute to local economies by reducing dependency on imports and increasing exports.
-
Sustainability
Well-maintained machines consume less energy and reduce waste, aligning with sustainable agricultural practices.
-
Reputation
Consistent quality enhances the mill’s reputation, attracting more business opportunities.
Common Challenges and How to Overcome Them
-
Lack of Skilled Technicians
Solution: Partner with a consultancy firm for training and support.
-
Limited Access to Spare Parts
Solution: Establish reliable supply chains and stock essential spares.
-
High Maintenance Costs
Solution: Invest in high-quality equipment that requires less frequent repairs.
Understanding the above challenges, partnering with Indian consultancy firms can help deal with them.
Conclusion
Maintenance is the backbone of efficient rice milling operations. For consultancy firms undertaking turnkey projects in Africa, emphasizing maintenance not only ensures project success but also builds trust and long-term partnerships with clients. By implementing best practices, leveraging advanced tools, and training personnel, rice mills can achieve operational excellence and contribute significantly to the agricultural value chain.