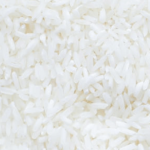
Understanding the Rice Mill Machine Flow
September 16, 2024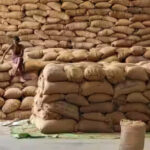
Indian Rice Mill Machine & the Rice Industry in Africa
December 25, 2024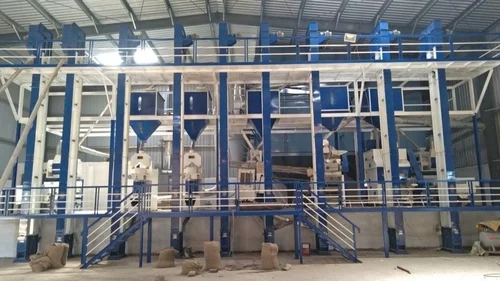
3 Best Practises for High-Quality Output from your Rice Mill Machine
Every grain of rice tells a story, and for millers, it’s a story of precision, efficiency, and quality.
From the moment the paddy arrives to the final polished kernel, the best rice mills are those that master the art of blending tradition with modern technology. Whether you're a mini rice mill or a large-scale operation, these best practices will ensure that your rice mill produces consistent, high-quality results.
Bonus- 3 common mistakes all rice mill owners are making!
According to the U.S. Department of Agriculture's Foreign Agricultural Service, Ghana's domestic rice production has been on an upward trajectory. It forecasts that Ghana's rice imports will increase to 900,000 metric tons in the 2024/25 marketing year, up from 850,000 metric tons in 2023/24.
*Click here to read the full report.
What is the considered a good output for a rice mill?
It is essential to understand some terms before we dive into the specifics:
- Head rice comprises milled rice kernels that are at least three-fourths the original length of the kernel; often referred to as “whole” kernels or “fancy.”
-
Milled rice is rice that remains once brown rice has been milled to remove the germ and a specified amount of the bran; this includes both broken and intact kernels (head rice).
*https://www.uaex.uada.edu/publications/pdf/mp192/chapter-14.pdf
While rice grades vary from one country to another (based on the market conditions & laws), in most ideal cases, the rice should have a minimum number of broken kernels.
A good rice mill will produce 50−60% head rice (whole kernels), 5−10% large broken and 10−15% small broken kernels. Typically, 5−25% broken kernels is acceptable.
3 Mistakes you should avoid while running your mill machines: Insights from mill owners
We spoke to mill owners and found the top 3 recurrent mistakes they all were making:
- Overloading: Especially the pre-cleaners. Across mill owners, we saw a common mistake of running their rice mill machines over capacity.
- Process Flow Planning: Lack of continuous flow process leads to increased processing team and wastage of product.
- Ignoring Automation: While automation can be an overall expensive affair, it is necessary to start automating the simple and repetitive steps. Automation works seamlessly in reducing costs for mills as the output is standardized.
Our Top 3 Good Practices for maximum productivity
(whether they are mini rice mills or large scaled rice machine mill)
- Good Quality Paddy - owners must maintain good supplier relations.
- Well Maintained Equipment- if regular upgrade of the systems is not possible, a regular maintenance of the existing machinery is of prime importance. Lack of upkeep results in higher operational costs and lower quality output.
- Well-Trained Operator- Employees should have appropriate skill to handle immediate breakdowns and for better upkeep of the rice mill machine. (Remember, well-trained employees are very different from well-educated employees).
Conclusion
By adhering to these best practices, you can boost productivity, enhance product quality, and achieve long-term profitability. Whether you're starting a new mill or optimizing an existing one, these strategies will position your business for success in a competitive market.
What steps are you taking to improve your rice mill? Share your thoughts and experiences in the comments below!